Мониторинг технического состояния подкрановых балок особо опасных производств с использованием ИИ для выявления трещин

Введение
Подкрановые балки являются важнейшими конструктивными элементами, используемыми в особо опасных производствах. Они обеспечивают безопасное перемещение кранов и грузов, и их надежность имеет критическое значение для обеспечения безопасности производственных процессов. Одним из наиболее распространенных и опасных видов повреждений подкрановых балок являются трещины в стенках, которые могут привести к катастрофическим последствиям. В связи с этим возникает необходимость внедрения современных технологий для мониторинга их технического состояния. Одним из таких решений является использование искусственного интеллекта (ИИ).
Проблема трещинообразования
Трещины в стенках подкрановых балок могут возникать по различным причинам, включая усталостные нагрузки, коррозию, неправильную эксплуатацию и дефекты производства. Раннее обнаружение таких трещин позволяет предотвратить аварийные ситуации и минимизировать затраты на ремонт. Традиционные методы контроля, такие как визуальный осмотр и ультразвуковая диагностика, требуют значительных временных и трудовых ресурсов и не всегда обеспечивают необходимую точность.
Роль ИИ в мониторинге состояния балок
Искусственный интеллект, а точнее методы машинного обучения и глубокого обучения, предоставляют новые возможности для автоматизации процесса мониторинга и диагностики технического состояния подкрановых балок. Система на основе ИИ способна анализировать данные с различных датчиков и обнаруживать аномалии, свидетельствующие о начале трещинообразования.
Предлагаемое решение
Предлагаемая система мониторинга технического состояния подкрановых балок с использованием ИИ включает следующие компоненты:
- Сбор данных:
- Датчики вибрации и акустической эмиссии устанавливаются на подкрановые балки для непрерывного сбора данных.
- Камеры высокого разрешения для визуального контроля поверхности балок.
- Обработка данных:
- Первичная обработка сигналов с датчиков для фильтрации шума и выделения значимых признаков.
- Анализ изображений для выявления поверхностных дефектов и трещин.
- Модель ИИ:
- Обучение модели глубокого обучения на базе собранных данных для распознавания паттернов, указывающих на наличие трещин.
- Использование сверточных нейронных сетей (CNN) для анализа изображений и рекуррентных нейронных сетей (RNN) для обработки временных рядов данных с датчиков.
- Интерфейс пользователя:
- Разработка интерфейса для визуализации состояния подкрановых балок в реальном времени.
- Система уведомлений для предупреждения о возможных трещинах и необходимости проведения инспекции.
Преимущества использования ИИ
- Повышенная точность: ИИ-системы способны обнаруживать трещины на ранних стадиях их формирования, что позволяет своевременно принимать меры по их устранению.
- Снижение затрат: Автоматизация процесса мониторинга сокращает потребность в частых инспекциях и уменьшает затраты на обслуживание.
- Непрерывный мониторинг: Система обеспечивает постоянный контроль за состоянием балок, что особенно важно для особо опасных производств.
- Масштабируемость: Решение может быть легко адаптировано для использования на различных типах производственных объектов.
Заключение
Внедрение системы мониторинга технического состояния подкрановых балок с использованием ИИ представляет собой инновационный подход к обеспечению безопасности особо опасных производств. Она позволяет не только повысить надежность конструкций, но и оптимизировать затраты на их обслуживание и ремонт. Благодаря современным технологиям искусственного интеллекта, мониторинг становится более точным, эффективным и доступным, что способствует улучшению общего уровня безопасности на производстве.
Еще больше новостей в нашем телеграмм канале

Опубликовано: Авг. 1, 2024, полночь Просмотры: 175
Комментарии
Отличная новость!
Опубликовано: Авг. 5, 2024, 8:39 д.п.Свяжитесь с нами
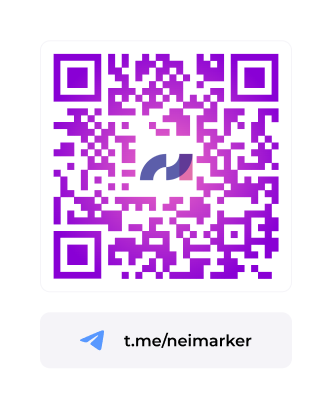
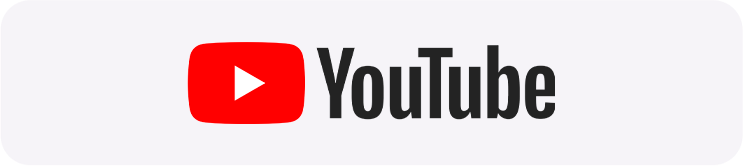